Full production in Poland
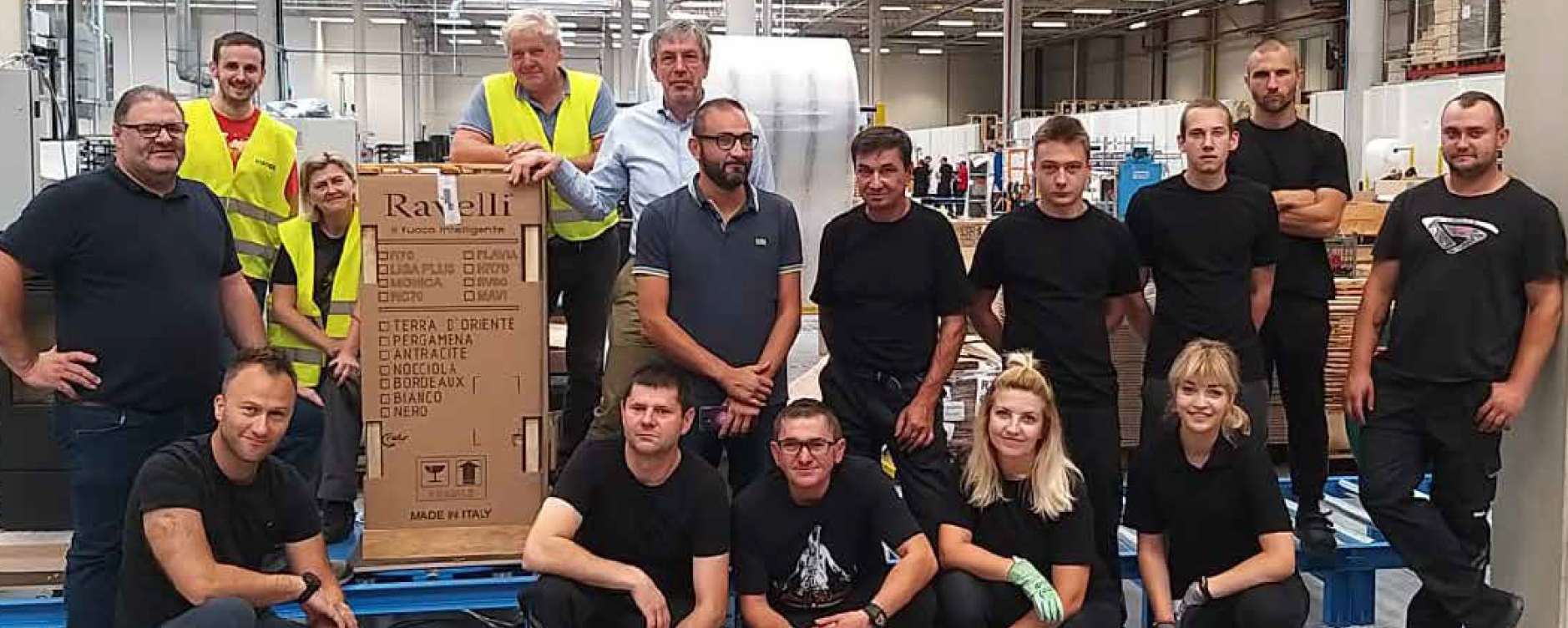
Built in record time – only 6 months – the production site wanted by the Jøtul Group in Poland is today a solid reality that can count on about 200 people working at full capacity.
The Wroclaw plant has in fact brought together the best of the northern European plants in a single “tailormade” 20,000 m2 building, to meet the specificities of the biomass heating sector. Thanks to an investment of about 7 million euros, the plant is equipped with the new state-of-the-art equipment and cutting-edge machinery including two lasers, a bending machine and a calender to cut and working on steel parts. As for the aesthetic workings, the site is equipped with two painting systems, one for enameling and two sandblasters.
The presence of this equipment directly in the factory guarantees control over the entire production process, allowing the Group to produce high quality products for all brands. The Polish production site as an add on to the Palazzolo site to increase production capacity and create synergies.
In the new Polish site, attention to health reaches the highest levels: the area dedicated to machining – CNC and milling machines, drills – has been isolated and placed in negative pressure to prevent dust from invading and dirtying the rest of the production.
We are convinced that the collaboration with the Wroclaw site will produce significant synergies and benefits. Firstly, the Polish site is already operational for the production of both steel stoves and cast iron stoves and, alongside the Palazzolo plant, it will significantly increase the Group’s production capacity. That is why a few months ago we started a training and coaching path for new collaborators, which is giving excellent results.
In addition, thanks to the collaboration with the Research & Development Office in Palazzolo, the Polish site has started the procedure to request and obtain the CSA certification in order to be able to produce models dedicated to the US market.
We are aware that the complete alignment of the two plants will take some time – particularly in the current situation due to the COVID emergency – but we know that we are working in the right direction.